Creating an effective ball cover requires meticulous engineering and thoughtful design. This blog explores the intricate details involved in designing a CAD model for a ball cover, showcasing our expertise and inviting potential clients to entrust us with their CAD and CAE needs.
The ball cover we designed has a radius of 44mm, providing a snug fit with an internal clearance of 0.5mm diametrically. This clearance is crucial for ensuring smooth operation and accommodating any minor variations in manufacturing. The design ensures that the ball fits perfectly within the cover while allowing for easy insertion and removal.
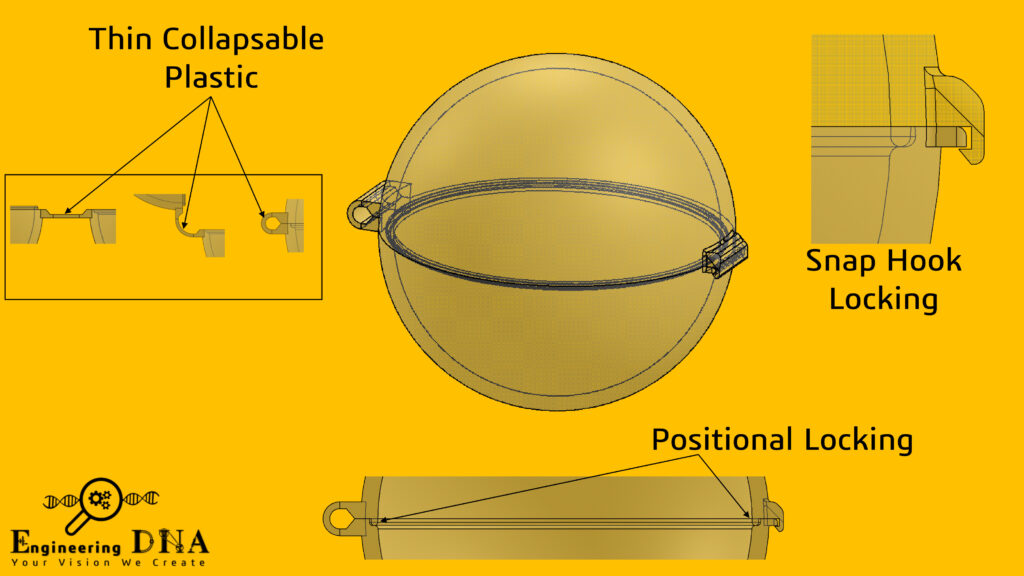
One of the critical features of our ball cover is the thin connecting wall between the top and bottom parts. This wall, when manufactured with plastic, is designed to fold seamlessly. At just 0.8mm thick, the wall is thin enough to be flexible yet sturdy enough to maintain its structural integrity. This delicate balance is achieved through precise engineering calculations and extensive testing.
The locking mechanism of the ball cover is another highlight of our design. We have incorporated a snap hook locking system that allows for effortless locking and unlocking. When a slight pressure is applied, the snap hook engages, securely locking the cover. Conversely, a gentle force will deform the snap hook, releasing the lock. This design ensures that frequent locking and unlocking can be performed with ease, making the cover highly user-friendly.
Maintaining the alignment of the top and bottom parts of the cover is crucial for its functionality. To achieve this, we have included a lip groove along the entire circular region of the cover. This groove ensures that the top and bottom parts remain perfectly aligned when closed, preventing any misalignment that could compromise the cover’s performance.
Our expertise in CAD and CAE is evident in the attention to detail and the innovative solutions we bring to our designs. From the precise measurements and clearances to the user-friendly locking mechanism and alignment features, every aspect of this ball cover has been meticulously engineered.
After the design phase, we employ 3D printing to create a prototype of the ball cover. This step allows us to verify the design’s functionality and make any necessary adjustments before proceeding to the final manufacturing process. 3D printing serves as a cost-effective way to ensure that the design is flawless, reducing the risk of errors during the injection molding process, which can be costly.
At our company, we pride ourselves on delivering high-quality CAD and CAE solutions to a diverse range of clients, including OEMs, government bodies, and various industries. Our team of skilled engineers and designers is equipped to handle projects of any complexity, ensuring that our clients receive the best possible outcomes.
We invite you to explore our services and discover how we can help bring your designs to life. Whether you need a simple component or a complex assembly, our expertise and commitment to excellence make us the ideal partner for all your CAD and CAE needs. Contact us today to learn more about how we can support your projects and help you achieve your goals.